The Importance of Using Caps and Plugs for Protection in Industrial Applications
Industrial environments are rife with potential risks to workers and the sensitive equipment at the heart of operations. From the smallest screw to the largest machinery, every component counts, and their protection is not just a matter of efficiency but also safety and longevity. Caps and plugs are pivotal in safeguarding machine parts against numerous hazards contributing to premature wear and failure. Below, we delve into how these small but indispensable accessories contribute to a secure and productive industrial landscape.
Ensuring Equipment Longevity with Proper Protection Methods
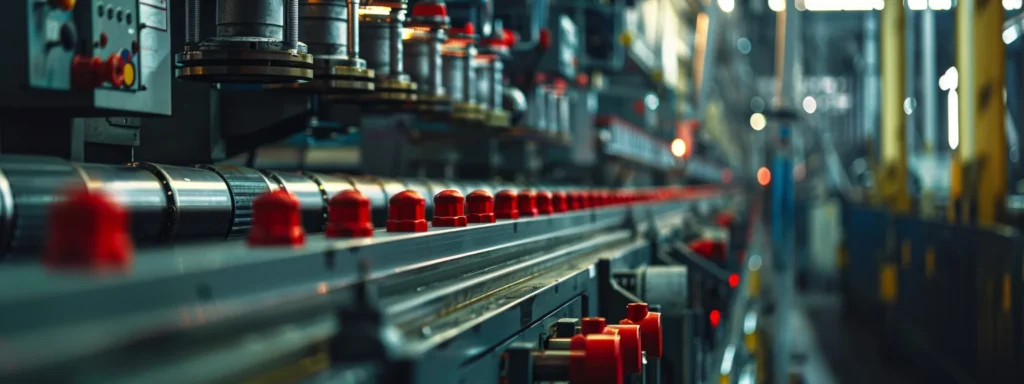
Equipment durability is paramount in the industry. Regular wear and tear is expected, but premature machine failure can halt production and result in revenue losses. Caps and plugs play a critical role in extending the service life of equipment by providing a protective barrier against dust, debris, and other contaminants that can cause internal damage.
By creating a seal over openings, these protection accessories can prevent moisture accumulation, leading to rust and corrosion. Even in harsh industrial settings, where chemical exposure is frequent, specialized caps and plugs can resist deterioration, safeguarding equipment parts from harsher elements to ensure continued operation without degradation.
Additionally, these protective devices maintain the integrity of pneumatic and hydraulic systems. By keeping out contaminants, caps, and plugs, they prevent blockages. They also maintain system pressures, ensuring that machinery operates within intended specifications and reducing the likelihood of malfunction or failure due to compromised components.
Effective protection strategies involving caps and plugs prolong equipment lifespan and reduce the frequency and severity of maintenance required. As a result, operations can anticipate a more predictable maintenance schedule, avoid costly repairs and replacements, and maintain a more streamlined production process overall.
The Impact of Environmental Threats on Industrial Components
Environmental factors significantly affect industrial components’ wear and operational efficiency. Dust, moisture, and extreme temperatures can all wreak havoc on unprotected equipment, leading to frequent maintenance issues and reduced lifespans. The strategic use of caps and plugs ensures these threats do not compromise machinery’s intricate workings.
For instance, UV exposure can degrade materials unsuitable for prolonged sunlight, leading to cracks, brittleness, and eventual failure. Caps and plugs designed with UV-resistant materials can protect sensitive outdoor equipment parts from the sun’s detrimental effects. Similarly, in coastal or marine environments, protection against saltwater corrosion becomes essential.
Electrical enclosures and circuitry are particularly vulnerable to dust and moisture. Using caps and plugs to seal off these sensitive components, companies can avert short circuits and other electrical failures from environmental exposure. The meticulous use of these simple tools is a testament to the philosophy that in industrial applications, the best defense is often proactive protection.
Furthermore, protective devices not only shield against the immediate dangers of operational environments but also contribute to a higher standard of product quality. Ensuring that the component surfaces remain unmarred by environmental factors means that the final products maintain their integrity, aesthetics, and performance from the assembly line to the end user.
Streamlining Maintenance with Effective Use of Protective Caps and Plugs
Regular maintenance is a non-negotiable part of industrial operations, ensuring equipment runs optimally. In this arena, caps and plugs are crucial in simplifying and expediting maintenance routines. They effectively block contaminants from entering critical areas, reducing the need for extensive cleaning or repairs.
Moreover, the simplistic design of caps and plugs allows for quick and easy application and removal, facilitating maintenance personnel’s work. These components can be applied during a machine’s downtime and removed just as easily before the system is powered back up, leading to a leaner and more efficient maintenance process.
In addition to protecting equipment internals during maintenance periods, these devices can be placeholders for repaired or replaced parts. This ensures that upon reassembly, everything aligns correctly, and the system functions as intended without hitches or disruptions in production flow.
The long-term cost savings from incorporating caps and plugs into maintenance programs are substantial. By preventing unnecessary wear and contributing to faster maintenance cycles, they help industrial firms avoid the steep costs of unexpected breakdowns and unscheduled stoppages, creating a more financially predictable operating environment.
Overall, caps and plugs are essential for protecting industrial equipment, ensuring longevity, and streamlining maintenance processes. By proactively safeguarding components against environmental threats and wear, these small accessories significantly enhance operational efficiency and reduce downtime.